Every hour, there are about 510 injuries reported at workplaces in the United States alone. These events can result in serious injuries and even death.
In economic aspect, millions of hours are lost to the effects of deteriorating workplace safety, findings made by a research paper writing service has revealed. Automatically, companies suffer from numerous compensations, medical treatments, and severance rates from these injured employees. Given these numbers, reinforcing accident prevention is critical. The best way to avoid this painful process is to invest in workplace safety.
As emphasized by different industries need security attention. In this regard, some suggestions may be of great value for maintaining employee protection parameters and measures. Check out these 10 steps to accident prevention in the workplace!
Steps to Take to Increase Workplace Safety
- Ensure the workplace tidy and organized
Many accidents occur due to the clutter on the desk. A tool dropped on the floor and a leakage on the floor can be costly. When these oversights add to the intensity of work routines, the result can be dangerous for everyone.
In this respect, little but simple care can make all the difference. Ensuring an organized workplace is the duty of all the workers. Teamwork results in a risk-free environment where everyone can move and act smoothly.
- Prioritize value for focus at work
All work needs to be done with focus. Especially in risky positions, it is critical to be aware of environmental factors that can pose safety hazards. With increasing forms of distraction, it is important to determine rules for worker protection and the priority with their obligations. According to assignment writing service, conversations, cell phones and even factors such as tiredness can expose workers to accidents.
- Avoid reckless risk exposure
Accidents often happen because of employees’ recklessness. If any situation demonstrates imminent danger, stay away from it. This thinking must be cultivated throughout the company so that it becomes a broad idea.
Do not visit places that you do not have prior permission to be there. Also, avoid getting around areas and equipment which you’re not qualified to use.
- Implement and ensure the use of Personal Protective Equipment (PPE)
The failure to use personal protective equipment can result in an unplanned cost of around £50m every year, according to a research by one of the dissertation writing services in the UK.
A company is required to provide, at no cost to the worker, all PPE that may be required in their operation. Employees will have different protection demands to perform their tasks safely.
Likewise, once the PPE is in the employees’ possession, he is obliged to use it, as well as to ensure their integrity. The company has a duty to provide and the right to enforce the use of PPE. These include gloves, goggles, breathing protection, hearing protection, fall belts, helmets, boots, among others.
- Take care of yourself and your co-workers
Accident prevention is a teamwork. It is necessary for co-workers to guide one another to avoid accidents. A good example is with the use of PPE as mentioned above. One employee must always remember and supervise the other to generate the right culture.
Another important thing is to avoid performing tasks in isolation, especially in hazardous areas. Follow-up, whether by another partner or a work safety technician, is important.
For this to work, it is important for co-workers to form partnership among themselves. Thus, the environment becomes safer and it strengthens the culture of accident prevention.
According to best essay writing services, unaddressed incidents can easily become accidents. Anything that happens out of the ordinary in your tasks should be communicated to your superiors. Typically, each company has its own incident reporting procedure, so it is critical to follow it.
Each experience will alert other people in the same situation. Future problems can be simply avoided by adopting corrective and preventive practices. Reporting incidents should be a habit. The more the company learns about them, the more it can work objectively to eliminate risks. This cycle tends to result in an increasingly safe work environment.
- Only use work machines that have been reviewed
Using serviced and certified machines is a good way of preventing accident. However, some companies do not always worry about a proper maintenance routine. Lack of time, cost, and the need to use them for tasks are factors that cause this problem. The employees, however, should not take any chances.
Every machine needs care and frequent overhaul. Else, it is susceptible to malfunctions that can lead to accidents. The problem will not always be limited to poorly executed work. The consequences can hit the employee who is using it. If you notice a problem, notify the maintenance guys about the need for maintenance. Regular reviews are essential.
- Avoid using tools in poor condition
Tools are also items that can create problems and should enter the accident prevention routine. They are subject to natural wear and tear, which can also endanger those handling them in everyday life.
It is essential that the employees stop using tools that are in poor condition, especially those exposed to impacts which can have consequences.
Breaking a cable, for example, can cause the worker to lose control, resulting in some shock to his own body. Injuries of different levels can happen and take the employee out of activity.
The proper thing to do is to introduce new tools and stop using those that are no longer efficient. As for the company, it is necessary to inspect the equipment regularly and arrange for replacement when necessary.
- Limit yourself to your duties only
Workers should not execute tasks which they are not trained for, especially those involving risks. Many industrial tasks require intensive training and courses, precisely what qualifies employees to perform them.
At no time should this practice be done. It is illegal, can cause accidents and harm the company. The employer should not ask an unprepared employee to do something they do not know how to do. Along with this, it is also up to the worker not to risk doing jobs that are not within his competence.
This negligence hinders accident prevention! If the employee is instructed to do something he or she does not know how to do, he or she should go to a superior or an occupational safety technician to report that he or she does not have the necessary qualifications.
- Operate machines responsibly
Machines are needed for various jobs in factories and large companies. Therefore, the operation requires basic usage parameters. Good practices range from attention when performing work to the use of PPE. Many machines are sharp, heavy and have other characteristics that, if not considered, pose serious risks.
It is then critical that the operator is primarily qualified to work with the machine. In addition, he needs to be very careful when operating, especially when other workers are nearby.
Conclusion
Accident prevention practice is extensive, but fundamental for the company and its employees. As pointed out in a workplace manual by good practices that increase workplace safety help make the workplace safer for everyone, curb downtime and therefore increase productivity.
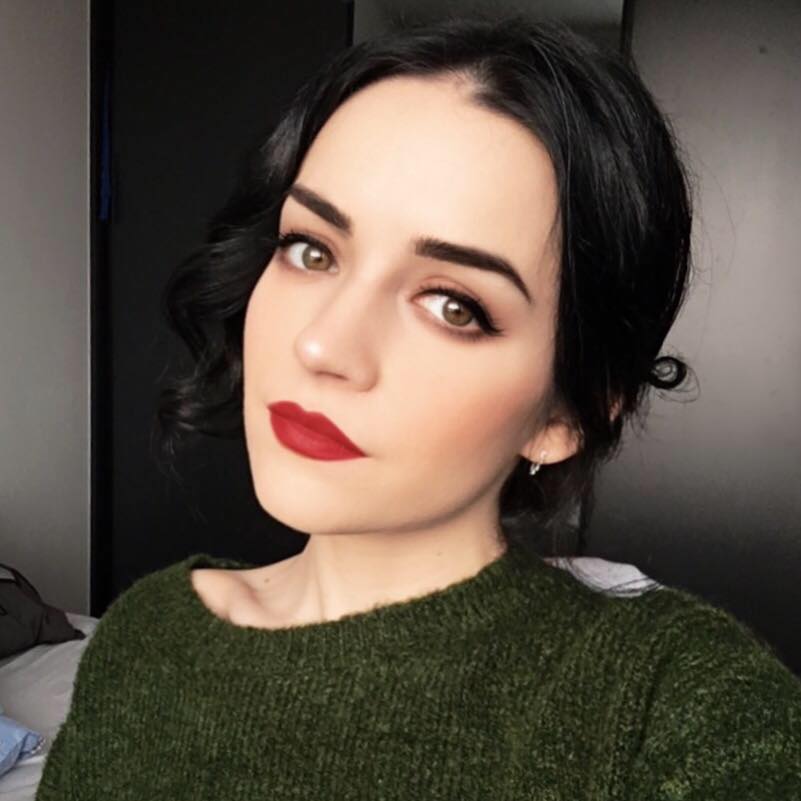
Author Bio
Sharon is marketing specialist and custom essay writer from Manchester, UK. When she has a minute, she loves to share a few of her thoughts about marketing, writing and blogging with you. Currently, she is working as a marketer at professional essay writers and essay-writing service. You could follow Sharon on Facebook.